Guide till Omrörare: Hjärtat i Blandningsprocessen
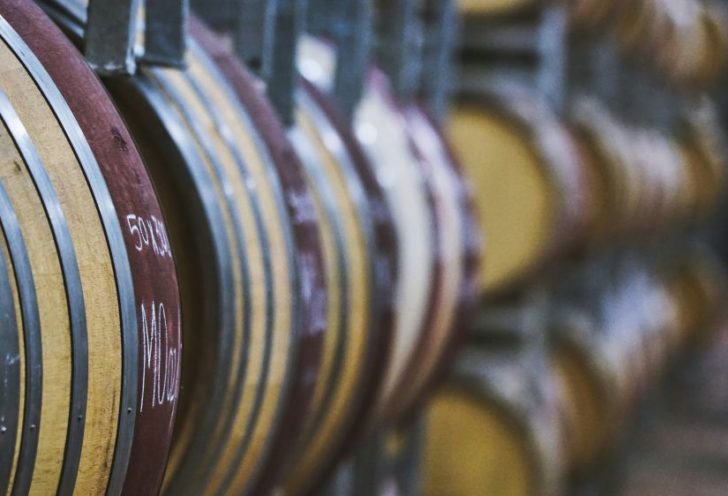
I industritillverkning och processindustrin är omrörare en central del av produktionssystemet. Dessa apparater är grunden för att säkerställa en homogen blandning av komponenter i en rad olika tillämpningar, från livsmedelsproduktion till kemisk tillverkning. Korrekt utvald och dimensionerad omrörare garanterar effektivitet, produktkvalitet och processtabilitet. Artikeln går igenom de viktigaste aspekterna av omrörare, från de olika typerna och deras funktioner till viktiga överväganden vid val av rätt omrörare för specifika tillämpningar.
Olika Typer av Omrörare och Deras Användningsområden
Omrörare kan kategoriseras efter deras design och de mekanismer genom vilka de blandar material. De huvudsakliga typerna av omrörare inkluderar propelleromrörare, turbinomrörare, paddelomrörare, och stativomrörare.
Propelleromrörare är liknande i form till båtpropellrar och är effektiva för att pumpa stora volymer av vätska. De är vanliga i applikationer där snabb blandning eller upplösning krävs. Turbinomrörare är ofta använda i mer involverade processer, som blandning av viskösa vätskor eller när det är nödvändigt med intensiv skjuvkraft. Paddelomrörare rör sig långsamt och är utmärkta för mild blandning av skörare ingredienser eller för att underhålla en konstant suspendering av fasta partiklar. Stativomrörare är en mångsidig kategori som kan designas för en rad olika applikationer, inklusive de som kräver stringent temperaturkontroll.
Design och Uppbyggnad av Omrörare
När man tittar på uppbyggnaden av en omrörare, är det centrala komponenterna motorn, omrörningsorganet (som ofta är ett blad eller flera blad), växellådan som styr rotationshastigheten, och axeln som översätter motorns kraft till omrörningsorganet. Dessa element måste vara anpassade för att arbeta ihop effektivt och för att passa den specifika applikationens krav.
Motorns dimensioner är avgörande och bör väljas baserat på den önskade blandningens intensitet och viskositeten hos de blandade materialen. Omrörningsorganets storlek och form är avgörande faktorer när det handlar om att skapa en specifik flödesmönster i tanken. Växellådan, å andra sidan, måste kunna hantera varierande belastningar och ha en tillräcklig varvtalsintervall för att uppnå optimal blandning. Axeln som binder ihop motorn och blandningsorganet måste vara tillräckligt stark för att hantera den stress som orsakas av omrörningsprocessen och materialets belastning.
Konstruktion och materialval i en omrörare är också kritiska. Rostfritt stål är ett vanligt material på grund av sin hållbarhet och korrosionsresistens. Andra material som kan användas beroende på användning är titan, olika plastmaterial, eller specialbeläggningar vid hantering av särskilt aggressiva kemikalier.
Tekniska Överväganden för Optimal Prestanda
Tekniska övre överväganden inkluderar val av drivsystem, rotationshastighet, och att designa flödesmönster och tankkonfiguration på ett sätt som maximerar omrörningseffektiviteten och minimerar energiförbrukningen.
Man behöver förstå de fysikaliska och kemiska egenskaperna hos de material som ska blandas för att välja rätt typ av omrörare. Viskositet, densitet, och lösligheten hos komponenterna är alla faktorer som påverkar valet av omrörningsteknik och utrustningens storlek.
Utvärdering av processparametrar, som blandningstid och temperaturintervall, är också centralt. I vissa fall måste omröraren kunna fungera under specifika miljöförhållanden, som under högt tryck eller i vakuum. Vidare måste omröraren designas för att minimera döda zoner i tanken där material kan stagnera och inte blandas ordentligt.
Underhåll och Säkerhet
Slutligen är underhåll och säkerhet kritiska aspekter när det gäller industriella omrörare. Regelbundet underhåll garanterar att omröraren fortsätter att fungera effektivt och undviker oväntade driftstopp. Detta kan innefatta inspektion och utbyte av slitdelar, smörjning av rörliga delar, samt övervakning av motor och kontrollsystem.
Säkerhetsåtgärder måste implementeras, särskilt i processer som involverar farliga material eller där det finns risk för övertryck eller explosion. Genom att följa gällande säkerhetsföreskrifter och säkerställa att utrustningen används på rätt sätt, kan riskerna minimeras.